PRODUCTION LOGGING BASICS
The primary objective of production logging is reservoir
performance evaluation or flow profile evaluation.
Production logging is a complex downhole logging
technique designed to allow us to determine flowrate, fluid
types, and fluid flow distribution in production and
injection wells.
Secondary production logging objectives are lift (or
completion) performance evaluation and estimations of
factors affecting the reservoir performance (leaks and crossflows).
The best known production logging tool is the flowmeter log.
There are 3 flavours of flowmeter: continuous or fullbore,
diverting, and array spinner flowmeters.
Other measurements are usually
needed to aid analysis, including:.
Temperature log
Radioactive tracer log
Noise log
Focused gamma ray density log
Unfocused gamma ray density log
Fluid capacitance log
Fluid identification log (in high angle wells)
Gradiomanometer (fluid density) log
Pressure sensors for static, flowing, build-up, and draw-down pressures
Gamma ray and collar log for depth control
See links on right-hand navigation menu to access these tool
descriptions.
Modern toolstrings include up to one
hundred various sensors, and processing techniques utilize
probabilistic non-linear algorithms of multiphase flows. The
basics are still the same as 40- 50 years ago, but they
have been brought into the 21st century..
Production logging is sometimes combined with well
integrity logging (multiarm calipers, ultrasonic thickness devices,
or serve itself as an indicator with temperature, flowmeter or noise
logging sensors) and cased hole formation evaluation logging (multidetector neutron logs, dipole
shear sonic logs, pulsed neutron logs with spectrometry
capability, natural gamma ray spectrometry logs) in through tubing
applications.
Production logging is usually carried out by the cased
hole wireline crew of the service company. That is carried
on wells of different definitions: production wells (on
different stage of the field development), injection wells
(with water, gas or steam stimulation), exploration wells
and wildcats (in combination with conventional DST),
hydrology wells and steam energy (geothermal) wells. When
the well is producer the test is known as production logging
test, when the well is injector – the test is known as an
injection logging test.
The number and sequence of production logging tests
performed on a well-managed field is defined by the field
development team. A good practice is to run the Production
Logs at an early stage of the life of the well, in
order to establish baseline that will be used later when
things go wrong. Too often Production Logs are run when
something has gone wrong as the last resort (to design well
interventions and workovers or even to take decision to
abandon the well).
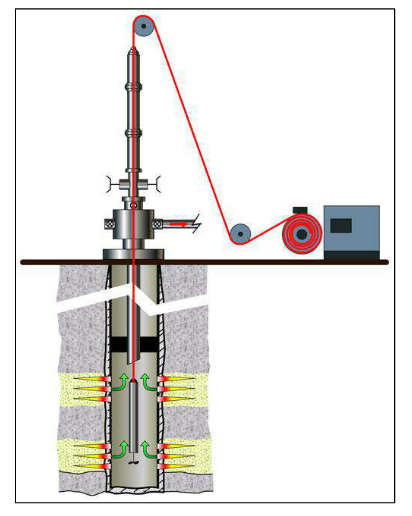
Schematics of Production Logging (KAPPA Eng. DDA handbook)
PLANNING A PRODUCTION LOGGING PROGRAM
A production
logging job starts with PL Survey design. A great amount of data is
gathered and analyzed. As much data as possible should be taken
into account: openhole logs, well integrity logs (CBL’s, Multi-Finger
tools, etc), deviation surveys, completion sketches,
production (pressures, temperatures, rates), and well intervention
history (recent operations). Don't forget the overall geology of the
reservoir and detail petrophysical analysis of the porosity,
permeability, and saturation profiles relative to the existing
completion type and location.
Most modern PLT jobs are run using 2 or 3 different flow rates and
several shut-in so as to provide a complete picture of the well's
performance capabilities. The main idea is to design a safe,
economical,
and comprehensive Production Logging Test.
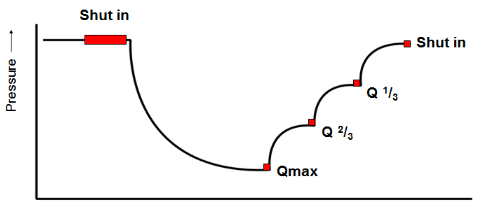
Typical PLT job sequence – flowing regimes and PLT
Surveys (marked with red dots). Well flowing rate regime is regulated by the
choke size (for natural flowing), gaslift injection rate (for
gaslift production), ESP power regulation (electric submersible pump
case – in this case special completion solution, known as Y-tool, is
required, otherwise logging below the pump is not possible) rod
pump power regulation (also special completion solution known as
“C-type” annulus is required for logging). For injectors, the
situation is the same.
The above example
illustrates 5 PLT surveys being performed (2 in shut in mode and 3
in flowing). Shut in survey (when the
well is closed at the surface) is used for downhole tool
calibration, pressure estimation, and possible crossflow evaluation.
In well-known fields, the
number of flowing regimes may be 2 with no shut in at all. However
in exploration wells (or wildcats), I have seen up to 7 flowing
regimes with direct and reverse measurements (increasing and
decreasing surface rate) and several shut in’s.
In some cases,
(low permeability rocks, shale gas formations, etc), the steady
state flow cannot be reached (or requires extremely long time for
well stabilizing). In this case, the advanced methods, known as
isochronal or optimized isochronal tests are being utilized.
PRODUCTION LOGGING RESULTS
Data processing software takes all the production log sensor
information and creates a production profile based on borehole
geometry (vertical, deviated, or horizontal) and the fluid phase
rates (one, two, or three phases). The math for this is not covered
here..
The
processed results are the pay zone's phase rate profile (total QZT,
interval QZI, relative QZTR) and selective inflow performance SIP diagram.
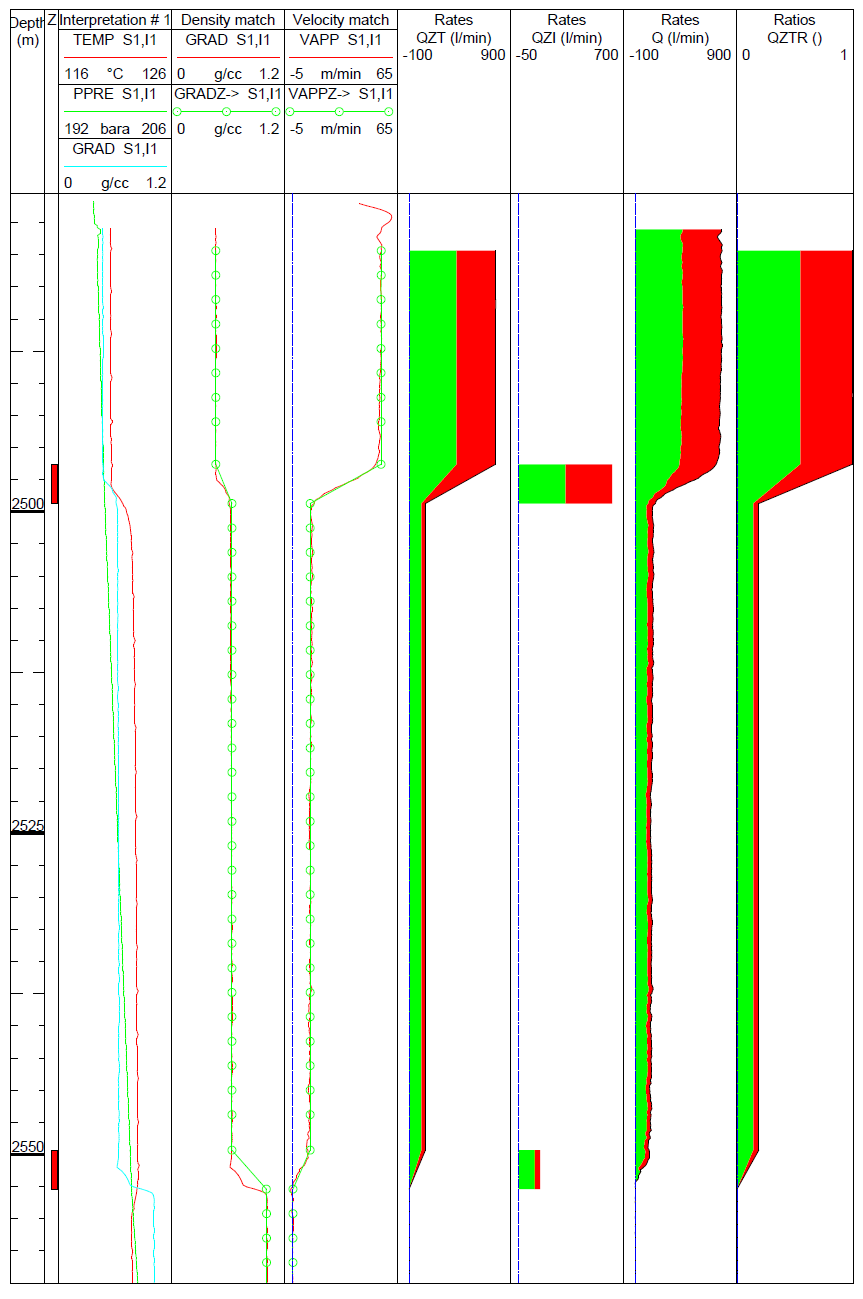
Results presentation of the conventional PLT Survey (Processed
with Kappa Emeraude)
Selective Inflow performance (SIP) diagram refers
to the pay zone producibility index estimation.
The total Inflow Performance Relationship IPR diagram, which is a
part of well testing steady state flow data interpretation,
reflects the pressure (or dP) as a function of total surface rate.
In contrast, the
SIP is constructed for every particular pay zone and flowing phase
for downhole conditions. SIP may be approximated with linear
equation, Vogel, Fetkovich or other inflow relationship (like 2,3 –
phase or gas inflow cases). The major purpose of this technique is
to evaluate the zone rate with particular pressure difference under
several conditions.
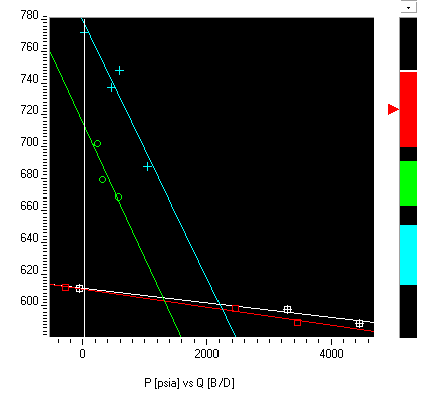 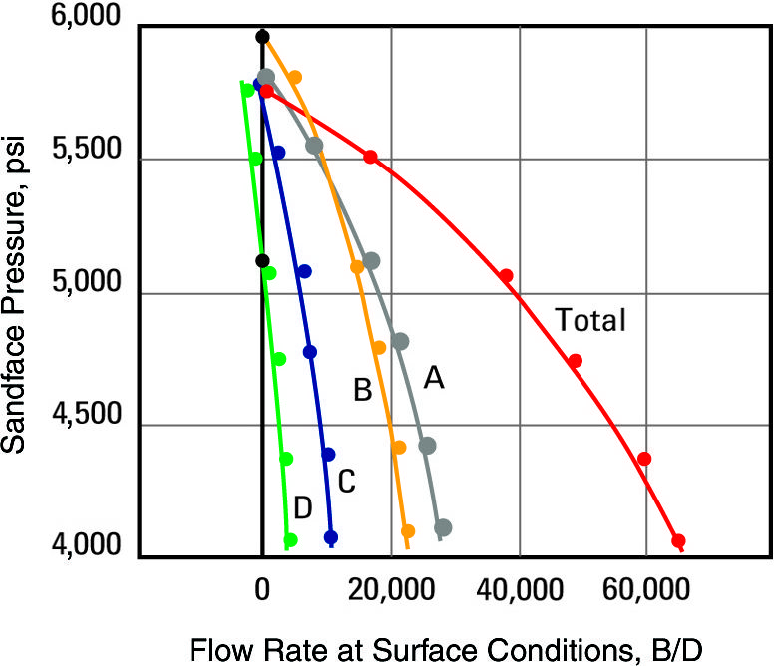
SIP Diagrams (linear approximation for 3 water pay zones with total
IPR colored with white – left and Vogel model for 4 oil pay zones
below bubble point pressure with total IPR colored with red – right,
Kappa Engineering and PetroWiki SPE examples)
SIP is
extremely useful reservoir engineering tool that provides an
opportunity to estimate reservoir pressure, producibility index,
possible zone crossflow and depletion for every pay zone and for
various fluid phases. To construct the SIP several well flowing
regimes (at least two) are required. Well flowing regime means the
well is producing with constant (steady state) or close to
steady state at surface. During the PLT, the surface multi-phase rates
are measured as usual and are used later for matching with downhole
data and velocity (flowing) model
PERMEABILITY FROM FLOW RATE
Once
actual flow rate at the formation is determined, reservoir
permeability can be calculated.
For linear horizontal flow, Darcy's fluid
flow equation relates flow rate to permeability as follows:
1: Q = 1.127 * A * (K / MU) * (P1 - P2) / L
Where:
Q = quantity of fluid (bbl/day)
A = area fluid flows through (sq feet)
K = permeability (Darcies)
MU = viscosity of fluid (centipoise)
P1 - P2 = pressure differential (psi)
L = length of flow path (feet)
For
oilfield work, fluid flow from a reservoir into a wellbore is not
linear but radial, so the equation becomes:
2: Q = 3.07 * H * (K / MU) * (Pr - Pb) / log(Rr/Rb)
Rearranging and solving for K:
3: K = Q * log(Rr/Rb) * MU / (3.07 * H * (Pr - Pb))
Where:
K = permeability (Darcies)
Q = quantity of fluid (bbl/day)
H = thickness of reservoir that fluid flows through (feet)
MU = viscosity of fluid (centipoise)
Pr - Pb = pressure differential from reservoir to wellbore (psi)
Rr = radius of reservoir = length of flow path (feet)
Rb = radius of wellbore (feet)
This
permeability
estimation should be calibrated with other data sources,
for
example pressure transient
analysis technique on pressure buildup or drawdown data, or the
geometric average of conventional core analysis data. Some skin-effect assumptions
may be
needed.
|