WIRELINE
FORMATION TESTING BASICS
This page describes wireline formation
tester tools profiles, in the order of their appearance over
the years. This presentation style provides insights into
tool evolution, and a specific tool’s capabilities and
limitations. You will find most these tool types in your
well files – here’s your chance to learn more about them.
Formation testing on wireline was
developed in the mid 1950's to provide a faster, safer and
less expensive method of formation evaluation than
conventional drill stem testing (DST).
FORMATION TESTER (FT) TOOL
The earliest formation tester (FT)
used an electro-mechanical-hydraulic pad system to obtain
good contact with the borehole wall, then a 2 bullet
perforation charge was fired at a single depth point. This
created a pathway for fluids to flow from the reservoir into
a chamber at the base of the tool.
The first formation tester could only be operated in
uncased holes.
Hydrostatic, shut-in, and flowing
pressures were measured and recorded as the test proceeded. During
the flow period, formation fluids flowed into a collection chamber.
When the test was completed, the chamber was sealed at maximum
pressure and the tool brought back to the surface. Built-in
“Get-away” guns were fired in the case of differential sticking. The
recovered sample was analyzed in the lab to determine the fluid
properties. Shut-in pressures were plotted versus depth to determine
pressure gradients, gas-oil, gas-water, and oil-water contacts, as
well as the location of over- and under-pressured reservoirs.
Over the years, tools such as the
Formation Interval Tester (FIT), the Reservoir Description Tool (RDT)
and the Modular Formation Dynamics Tester (MDT) chart the evolution
of wireline formation testing. Each service company devised their
own tools and trade names. Tool development was driven by the need
to acquire single phase,
uncontaminated samples of reservoir fluid returned to surface. For
example, newer tools take multiple samples and allow the operator to
pump fluid from the reservoir instead of relying on natural flow
rates, permitting the tool to bypass the sample collection chamber
until a representative sample is obtained. This reduced the impact
of mud filtrate contamination on the final collected sample.
Along with pressure tests and
gradients, lab analyses of PVT relationships, GOR, viscosity, and
composition are the foundation for planning production and
processing facilities. The following overview of tools shows how
wireline testing has evolved to provide a clearer picture of
reservoir conditions.
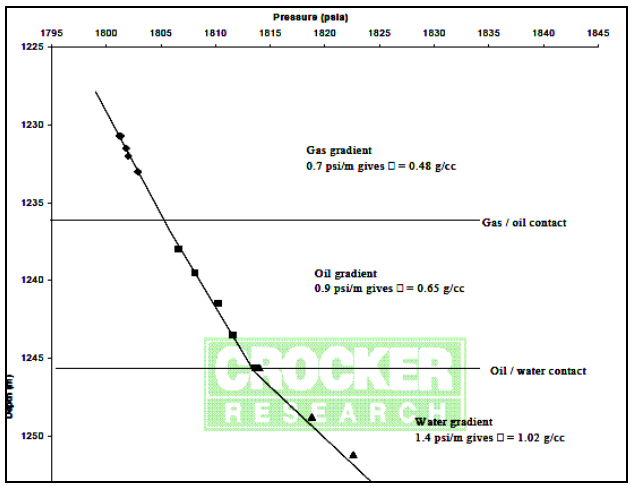
Graph of Shut-In Pressure versus Depth showing different pressure
gradients over the reservoir, indicating different fluid densities.
Gas-Oil and Oil-Water Contacts are marked at the changes in slope on
the gradient graph. It is sometimes difficult to see the change in
slope - try placing the graph horizontally at eye level and sighting
along the line. This is called the "Ant's-eye View". The bends in
the line are much more obvious.
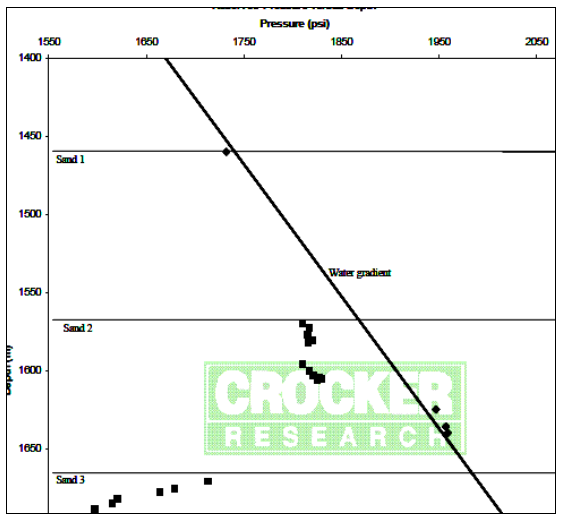
This graph shows partially depleted reservoir pressures, with some
pressure isolation between the upper and lower sands. A gamma ray or
image log on the graph would help to distinguish reservoir
boundaries and internal barriers.
(Illustrations courtesy Crocker Research)
REFERENCES:
A Method of Formation Testing on Logging Cable,
M. Lebourg, R.Q. Fields, C.A. Doh,
SPE-701-G, 1959.
Innovations in Wireline Fluid
Sampling,
Alastair Crumble et al
Oilfield Review, , Autumn 1998, pg. 26 – 41.
FORMATION
INTERVAL TESTER (FIT)
The first formation tester (FT) was developed to test
unconsolidated, soft rock in 7 7/8” open hole and claimed about a
50% success rate. The Formation Interval Tester (FIT) was developed
to test 5.5” cased hole completions, and to resolve poor sample
recoveries from hard, low-permeability formations.
The FIT simultaneously detonated two
perforations at an 8.5” spacing, testing a 1 foot interval of
formation rather than a single depth point. The 4.4” slim tool was
rated to penetrate ~3” of steel while the regular tool, with it’s
larger charge size, was able to penetrate over 4” of casing, or up
to 12” of formation. Dual packers sealed the FIT to the formation
wall, plus an automatic seal valve closed the sample chamber in the
event of seal failure. Like the FT, several chamber sizes were
available: 1, 2 ľ or 5 ˝ gallon. The deeper penetration, plus
better sealing function increased the chance of recovering fluids in
low permeability, hard formations and opened up formation testing
for use in cased holes. The FIT was not recommended for use in
unconsolidated formations.
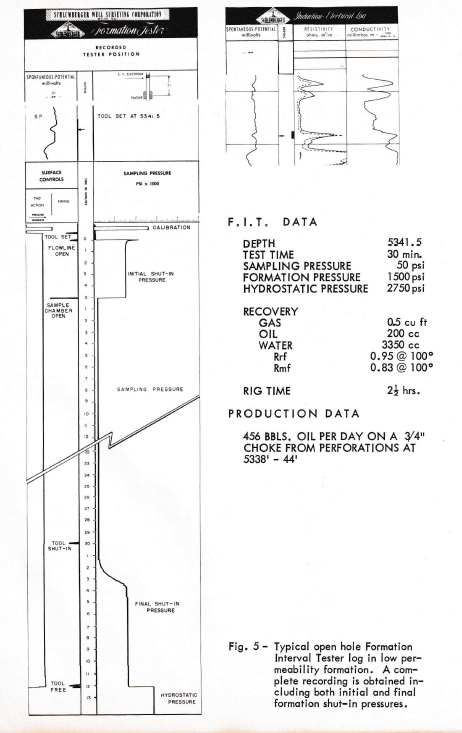
Plot from FIT showing recorded tester position calibrated to SP,
with Surface Control display marking the tool operations and
Sampling Pressures showing initial and final formation shut-in
pressures.
FORMATION
EVALUATION TOOL (FET)
The Formation Evaluation Tool (FET) was developed by Crocker
Research in Australia in the late 1980’s and is widely used by other
service companies under license. Its foremost feature is its ability
to pump from the formation until a representative sample is present,
that is until the characteristics of oil, gas, or water are
exhibited in the resistivity, conductivity, and density sensors of
the FET. Once a representative sample is flowing through the tool
the FET has the ability to capture a predefined volume of this
sample. This predefined volume is based on the multisampler
configuration which is set prior to down-hole operation.
In addition the FET contains two
Quartz Pressure Gauges which have an accuracy of 0.01 psi. This in
conjunction with the tools pumping ability allows for accurate
shut-in pressures (SIPs) to be obtained with controlled draw downs.
The FET pump can be manually controlled enabling any user defined
draw down volume to be acquired, lowest being 1cc. In addition the
FET has the ability to reverse pump, that is pump fluids from the
borehole into the formation.
The proven benefit of reverse pumping
is the tool’s ability to “pump off” the formation, beneficial for
situations where the tool has been set for long periods of time. The
FET has been designed such that if there is a loss of tool power for
whatever reason the tool will automatically retract (unset itself
from the formation) enabling it to be retrieved via the wireline
cable.
During the operation of the tool, the
operator is able to give the following information to the client:
For Pretests;
·
Draw Down Pressure (DDP) in PSIA,
·
Draw Down Volume in cc,
·
Shut In Pressure (SIP) in PSIA,
·
Fluid temperature in °C,
For Constant Flow Tests (for every
litre pumped);
·
Resistivity in ohm/m, Conductivity in mho/m,
·
Density in g/cc,
·
Temperature in °C,
·
Reservoir pressure in PSIA,
·
Flow rate in L/min,
·
and Permeability in mDarcy.
For each sample taken;
·
Resistivity in Ohm/m,
·
Conductivity in mho/m,
·
Density in g/cc,
·
Temperature in °C,
·
Reservoir pressure in PSIA,
·
Flow rate in Litres/min,
·
Permeability in mDarcy,
·
Pressure at surface in PSIA,
·
and Volume captured at surface in cc.
The primary purpose of a constant flow
test is to ensure that an uncontaminated sample of the Reservoir
fluid or gas is flowing through the tool. During a constant flow
test, for every litre pumped the resistivity, conductivity and
density of the hydrocarbon or water is monitored in search for a
“breakthrough”. Meaning, when all the mud filtrate has been pumped
from the reservoir and the actual uncontaminated hydrocarbon or
water is present. When this occurs there is a noticeable difference
in the FET’s sensor readings which corresponds to the properties of
the hydrocarbon or water expected. It is at this stage that a sample
is taken upon the client’s request. Therefore, a constant flow test
must be performed before a sample is taken to ensure a
representative (uncontaminated) sample is taken.
Secondarily, a constant flow test may
be performed to gather the properties of the hydrocarbon or water
present after breakthrough in terms of resistivity, conductivity and
density. This may be used to confirm the depth pressure gradients as
well as reservoir contact depths.
In addition to this, a constant flow
test also results in the flow rate and permeability of the fluid to
be determined.
Reservoir fluid samples are captured
within the multisampler component of the FET. The configuration of
the multisampler depicts the quantity and volume of samples
captured.
The FET has the capability of
attaching a PVT sampling assembly to the bottom of the tool to
capture 2 x 524.4cc formation fluid samples per run.
Before any pretests are performed the
tool packer must be set at the correct depth. This is achieved via a
gamma ray plot. A gamma ray plot is printed and correlated with an
existing gamma ray plot and the packer depth adjusted accordingly.
The requirement for the gamma ray correlation is that the FET
Software must be connected to the logging unit’s depth system. The
FET Software can connect to the logging unit’s depth system via an
RS-232 serial port.
Once the down-hole job is completed,
the end result in the FET Software is a graphical log illustrating
all sensor measurements over time for pretests, constant flow tests,
and samples captured. The client receives a hardcopy and a data file
in LAS format. Examples are shown at the end of this webpage.
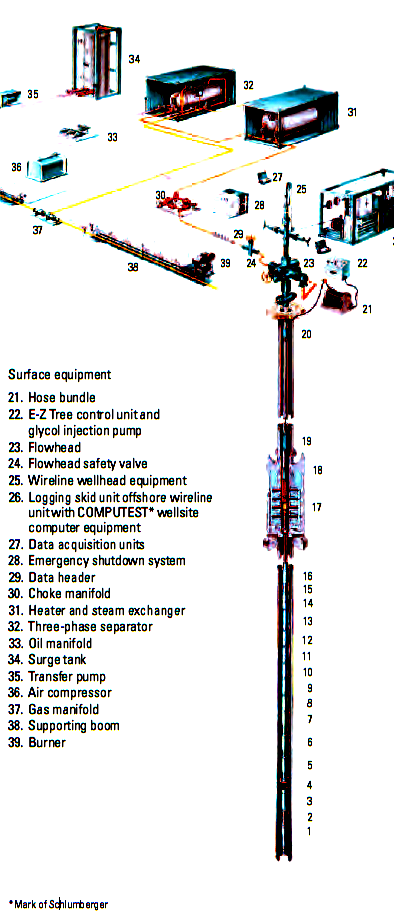
Diagram of a Schlumberger MDT formation tester.
MODULAR DYNAMIC
FORMATION TESTER (MDT)
Schlumberger’s Modular Dynamic Formation Tester tool (MDT)
exemplifies a modular approach to suit different reservoir types and
to ensure recovery of monophasic samples. The MDT is powered by an
electronic power cartridge which converts AC from surface to DC to
power all modules. An hydraulic power module sets/retracts probes
and is used to prevent differential sticking. A dual-purpose
pump-out module removes unwanted filtrate before sampling and
inflates packers.
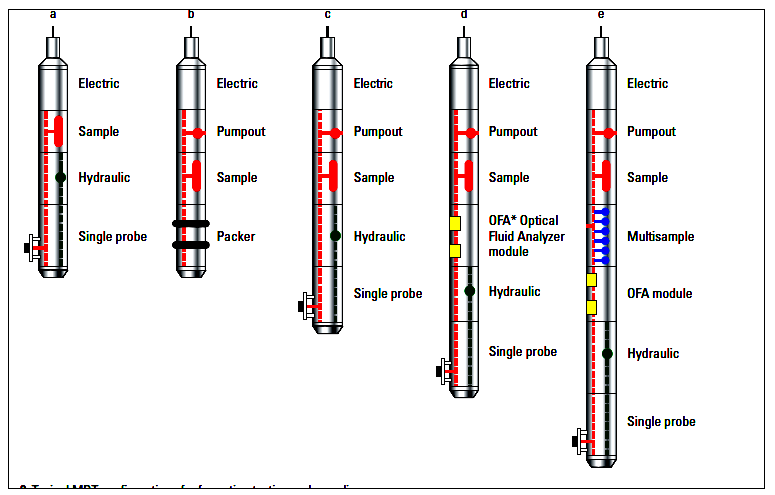
Today’s formation testers can be configured in various ways to suit
the test requirements. (illustration courtesy Schlumberger)
The operator can choose a Single or
Dual-probe module depending upon the answers required. A basic
configuration for pressure, vertical permeability and sampling,
could combine several Single-probe assemblies with six sample
chambers set at the base of the tool. The Single-probe module
consists of packer and telescoping backup pistons, pressure gauges,
sensors for fluid resistivity and temperature plus a 20 cc pretest
chamber. The module has a strain gauge and a CQG (Crystal Quartz
Gauge) that allows monitoring of drawdown from surface.
When used in tandem with the
Dual-probe module, pressures are measured by both the Single and the
Dual-probe, the latter featuring two probes mounted back to back on
the same block, at 180 degrees, giving horizontal permeability. The
multi-probe configuration provides data for near wellbore
permeability anisotropy, or running interference testing to assess
communication between adjacent horizons.
The Probe/Dual-Packer Module, with two
inflatable packers isolating an interval of 3-11’, ensures that
fluid can be withdrawn at a greater rate without dropping below the
bubble point. The larger interval results in a radius of
investigation up to 10 feet into the reservoir for better
permeability estimates. The Flow Control Module allows formation
fluid to flow into a 1 liter pretest chamber, useful for tests which
require a controlled flow rate.
A Single-Phase Multisample Chamber
used with the Multi-Sample Module enables monophasic fluid
collection for PVT analysis. The sample is pressurized by Nitrogen,
to stop phase alterations due to temperature induced pressure drop
as the chamber is returned to surface.
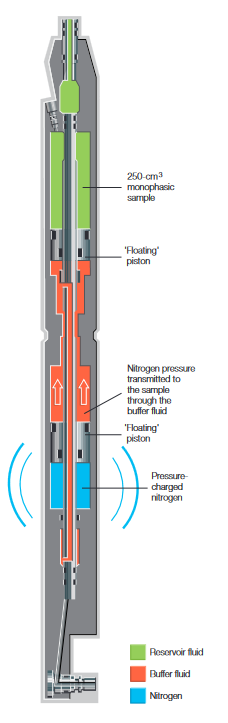
Multisample Chamber showing Nitrogen Pressure component which allows
the sample to be pressurized but not contaminated by the element.
Possibly the most innovative module is
the Live Fluid Analyzer, used to pinpoint when the fluid becomes
least contaminated by filtrate, particularly that of Oil Based Muds
(OBM), or in cases of deep invasion. Using a near-infrared
spectrometer, the LFA (or Optical Fluid Analyzer - OFA) measures
optical properties of the fluid in the flowline. Gas is detected by
measuring polarized light reflection. When optical readings indicate
that the amount of mud filtrate has stabilized at a low value, the
sample is taken. The tool also discriminates between oil and water,
and crude oil versus OBM.
As oil exploration requires ever
greater finesse, tools such as MDT Forte and MDT Forte-HT have been
developed for use in rugged and high temperature environments.
Rugose/unstable boreholes, thinly laminated formations and sampling
low mobility/heavy fluids can be tested using the Saturn 3D Radial
Probe system. With multiple self-sealing ports, this tool provides
temporary mechanical stabilization of the reservoir walls and a
pressure differential great enough to mobilize heavy oil.
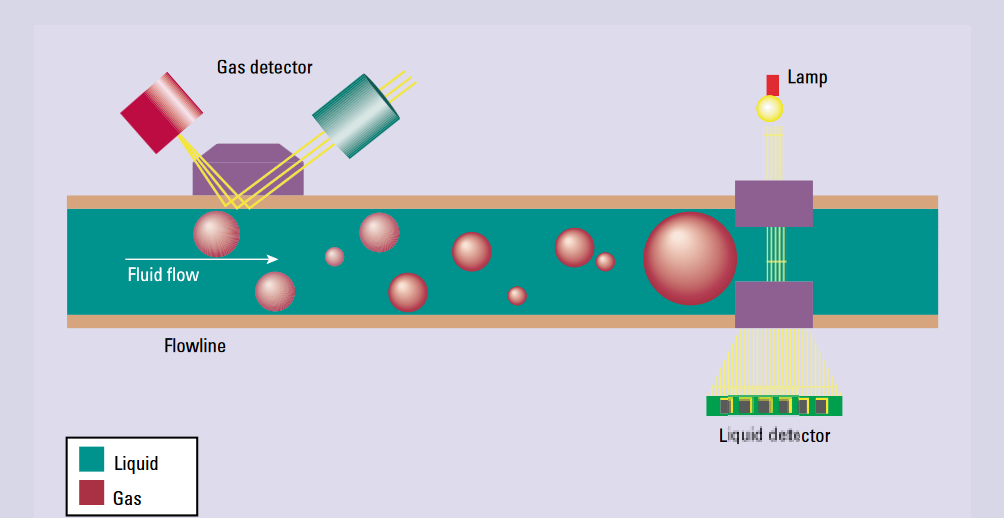
Diagram of Schlumberger LFA module gas detector and spectrometer.
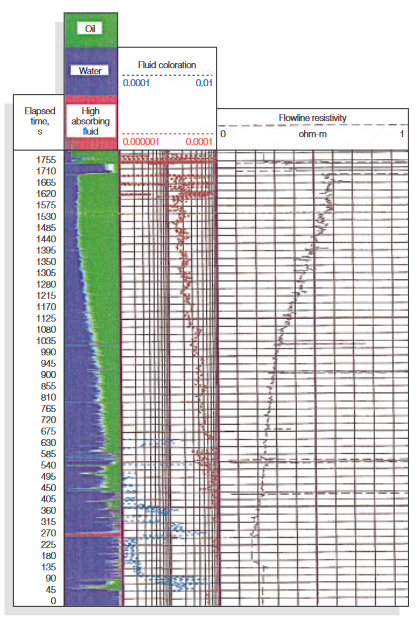
wing elapsed time (track 1) seal failures (exemplified by red spike
on track 2 at 270 seconds, – high absorbing fluid), and a
stabilizing of ratio between oil and water at 1440 seconds, with
corresponding decrease in coloration (track 3) and increase in
flowline resistivity (track 4). Sample was taken at 1440 seconds
and confirmed a 30% water cut.
FORMATION TESTER
EXAMPLES
The following examples of FET log presentations is courtesy of
Crocker Research.
EXAMPLE
1:
High permeability sand with light oil.
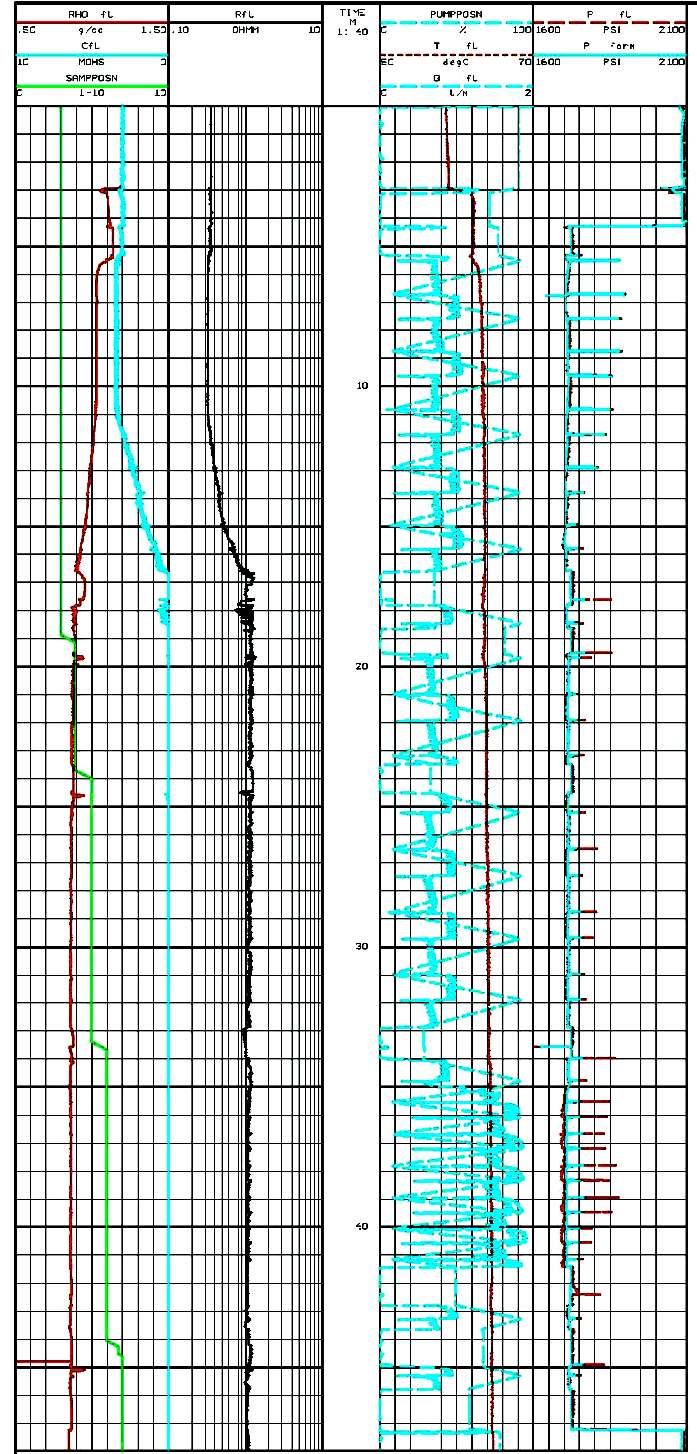
This is probably the easiest test. Oil breakthrough occurred only
six minutes after steady state flow began. Multi rate testing was
done which allows a plot of flowrate Q versus pressure drawdown.
Four samples were taken, all contained light oil.
EXAMPLE 2:
Low permeability sand with low viscosity oil.
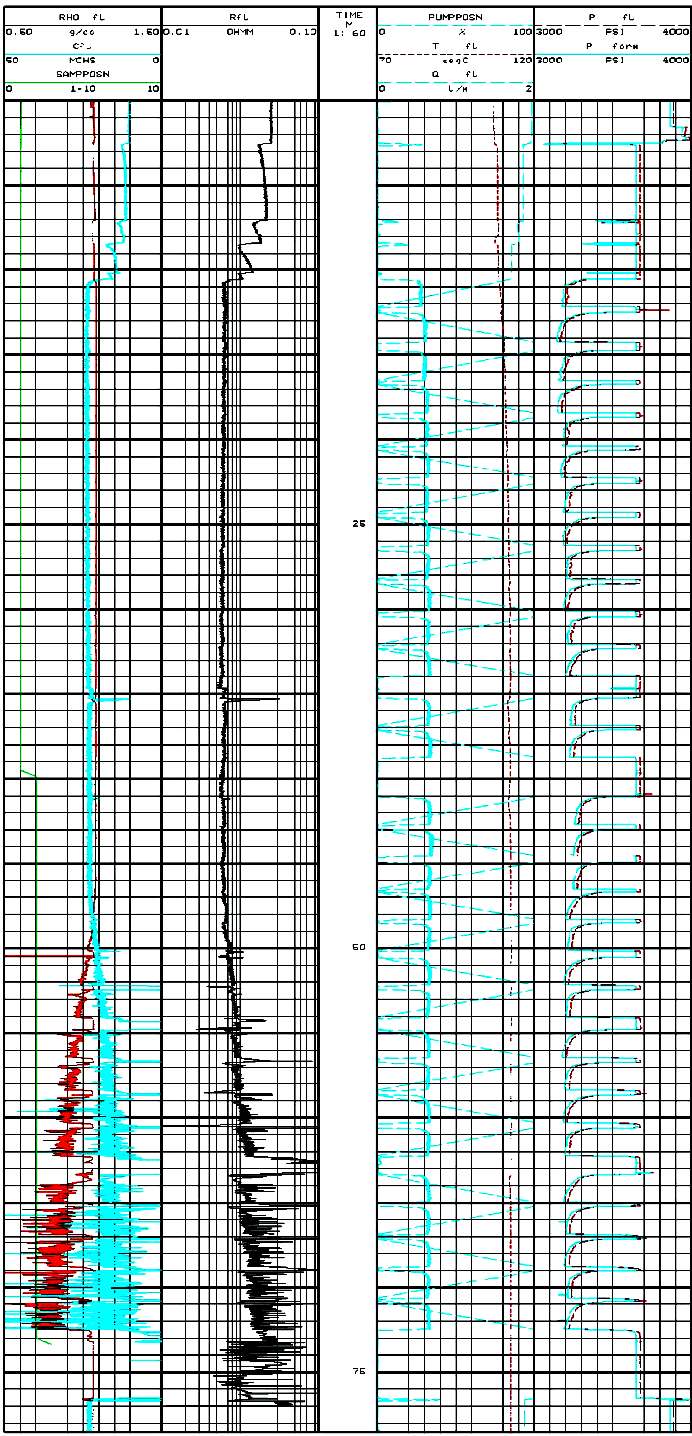
Large pressure drawdown was required to obtain 630 ml/min flow rate.
Oil breakthrough occurred after thirty-seven minutes of steady flow
(from the commencement of pumping). One filtrate and one oil sample
were taken. Permeability can be calculated from the pressure
drawdown or buildup curves. Note the marked difference between the
pretest buildup and the drawdown curves.
EXAMPLE 3:
High permeability loose sand with viscous oil.
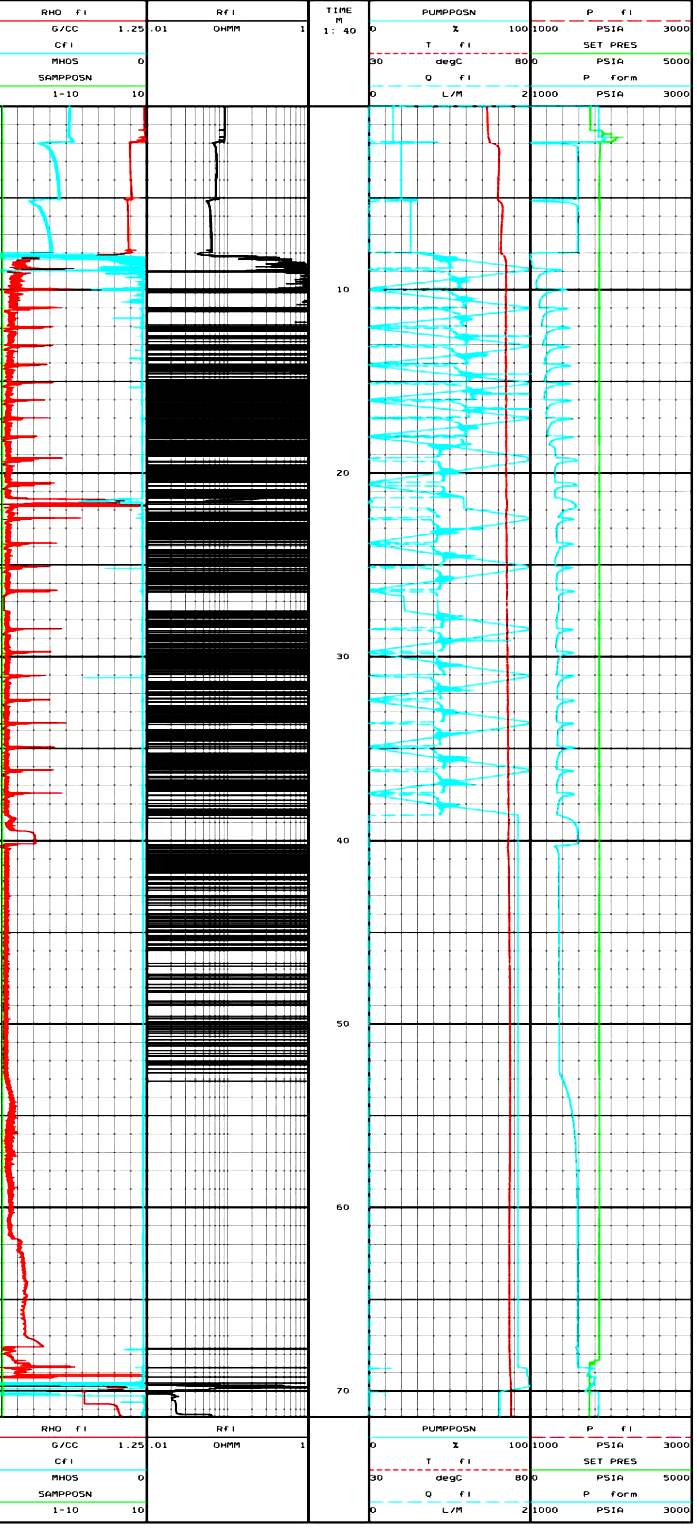
This is most interesting. All previous attempts in these
unconsolidated sands with other wireline test tools had failed
because of lost seals. We were asked if the FET could sample with a
minimum flowrate even if several hours of testing were required.
This test was done with only 14 psi drawdown and a flow rate of only
33ml/min. After some seven hours we had only taken 13 litres of
formation fluids. Oil breakthrough occurred after some 80 minutes of
steady flow (from the commencement of pumping). Slug flow occurred
resulting in the spiky resistivity, conductivity and density logs.
Despite the sanding problems the tool moved the formation fluids
steadily until after some five hours, sanding effects show steps on
the pump motion. Nine samples were taken and heavy oil and some
filtrate was recovered. Despite the long test the tool came free
with only a minimum overpull. Conventional large cylindrical sample
chambers present a large area for differential sticking. The FET
involves no such chambers and thus is unlikely to be differentially
stuck. Moreover, the tool is pumped off the wall once the tool is
retracted.
EXAMPLE 4:
Moderate permeability sand with viscous oil.
The
fourth possibility. Oil breakthrough occurred after about
thirty-five minutes of steady flow. Pressure drawdown was 107 psi at
a flowrate of 880 ml/min, which equates to a drawdown permeability
of 380 mD. After oil breakthrough the pressure drawdown increased to
486 psi at 720 ml/min. Assuming no relative permeability change
(which may not be valid) and a water viscosity 0.5 centipoise then
the oil viscosity is 2.75 centipoise. Please note that the oil
density is shown as 0.96 g/cc which checks well with the known
density. Four oil samples were taken.
EXAMPLE 5:
Gas sampling.
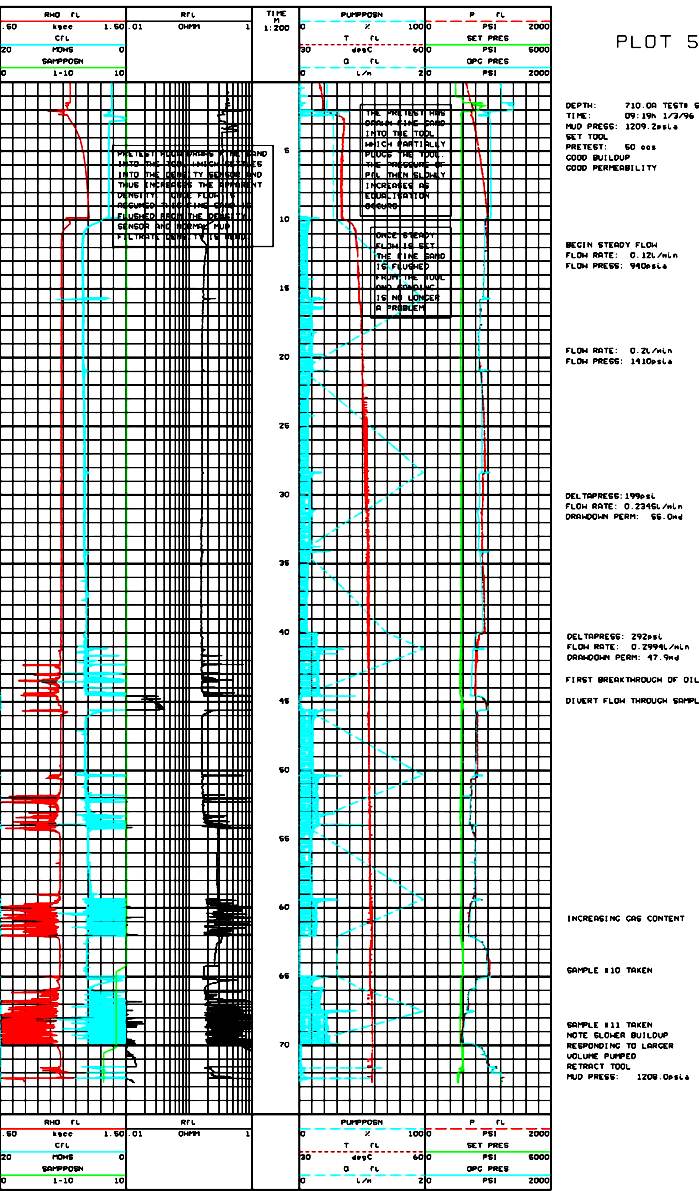
Care is taken to pump as little gas into the borehole as possible.
Although we have often sampled gas; no problem has ever been had
when circulating after testing. Gas breakthrough occurred after
thirty minutes of steady flow. Thereafter gas increased with time
but, curiously not at low flow rates. Two gas samples were taken.
The down-stroke of the pump (0.3 l/min) was at a higher rate than
the upstroke (0.2 l/min). It is clear that at 0.2 l/min flow rate
the filtrate supply from vertical flow in the formation is enough to
meet the FET flow rate and no gas enters the tool. At 0.3 l/min the
vertical flow rate of filtrate is not enough to meet the FET flow
rate and thus gas enters the tool. The final pump stroke is at 0.45
l/min and the highest gas flow rate occurs. Clearly the gas fraction
of flow is rate sensitive.
EXAMPLE 6:
Gas/Oil contact definition.
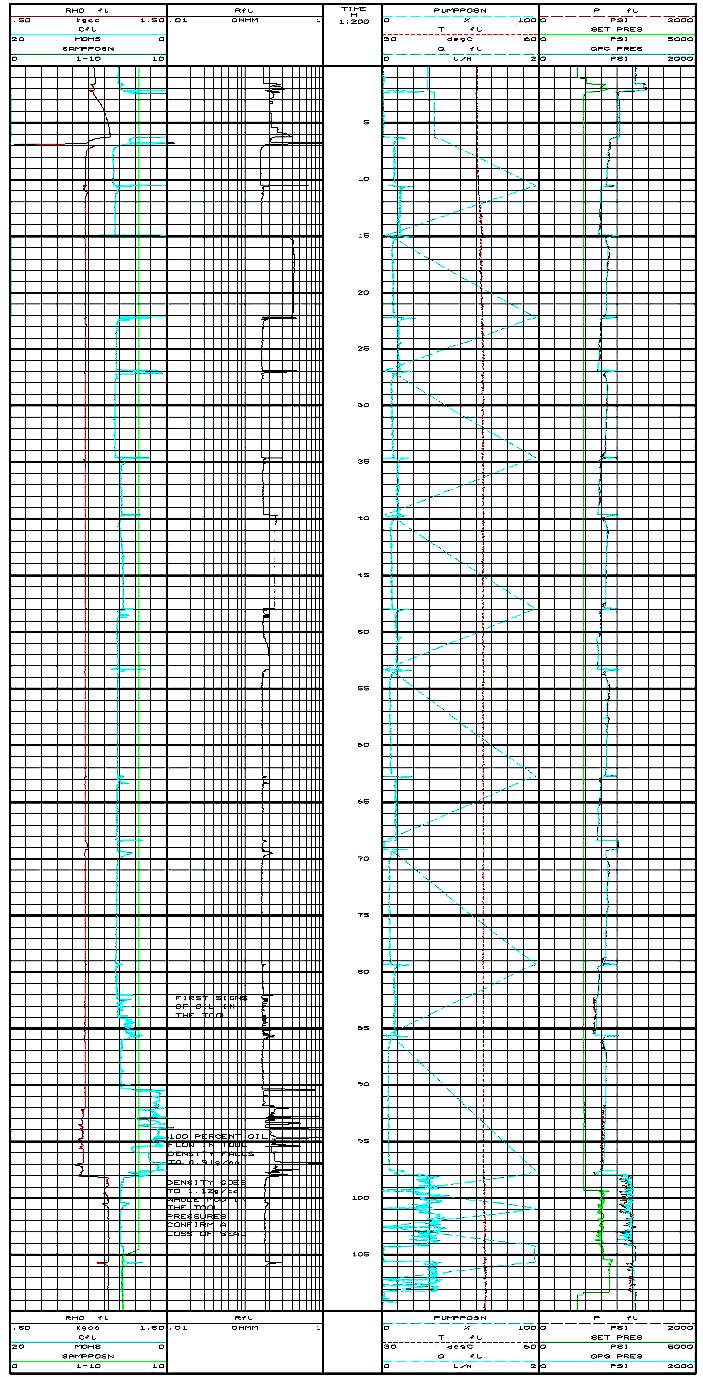
This test was taken three metres below Example 5. Oil breakthrough
occurred after eighty minutes of steady flow.
Oil density was 0.98 g/cc and contrasts strongly with the gas of
Example 5. This oil is heavily biodegraded, the light ends have been
removed by bacteria. Thus the oil is very under-saturated. This is
curious since the gas is in contact with the oil. It seems likely
that two stages of hydrocarbon migration have occurred, one of oil
and a later one of gas.
EXAMPLE 7:
Halliburton SFT with FET, Gas sampling.
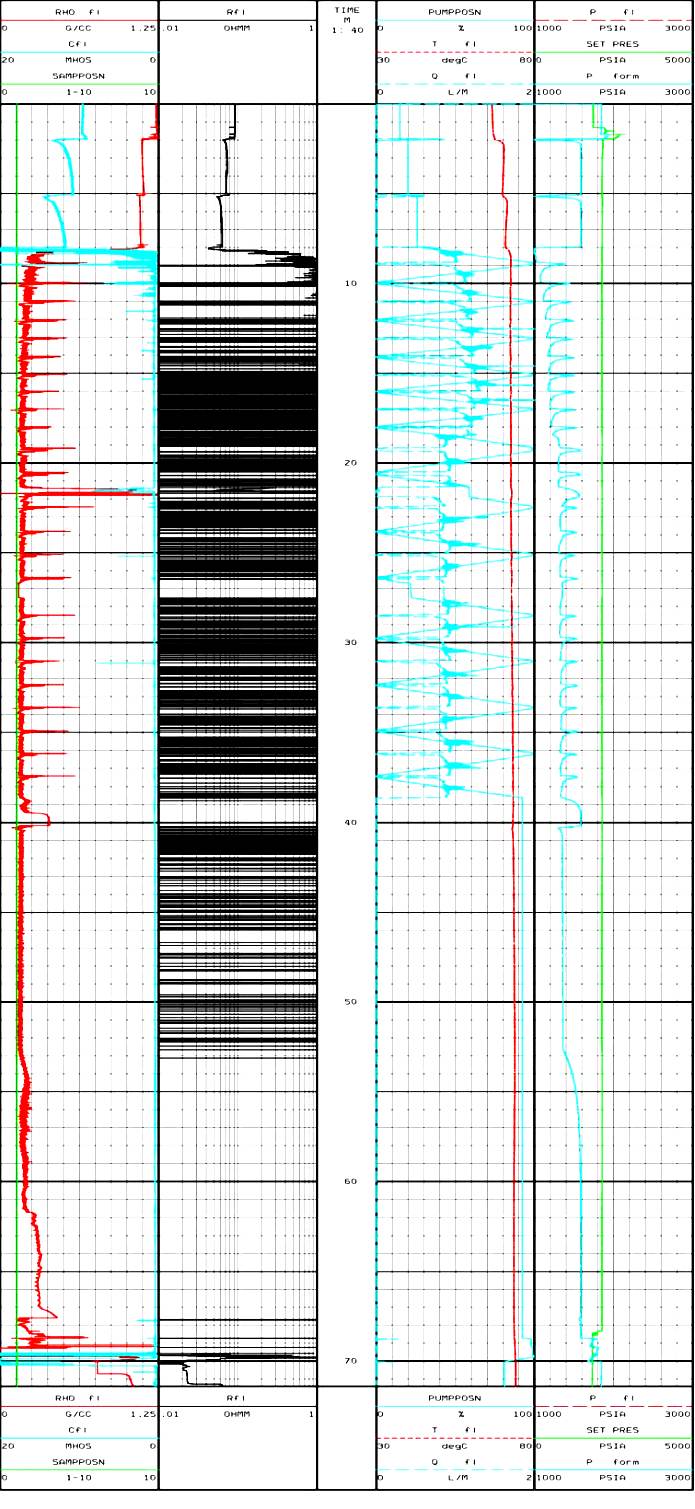
This test was the first commercial use of the SFT chambers in
conjunction with the FET. 25 litres pumped in 31 minutes before
diversion into SFT chamber. Flowing pressure ~200 psi below shut in
pressure. Chamber filled in ~12 minutes. Note the slow pressure
build-up when chamber fills. This is consistent with a compressible
fluid in the tool. Minimal filtrate in sample at surface. High
quality sample produced. Normal operation of the SFT is to open the
Chamber after pretest. The advantage of the FET is the ability to
removed an unlimited amount of fluid before sampling commences.
EXAMPLE 8:
Halliburton SFT with FET - Water sampling
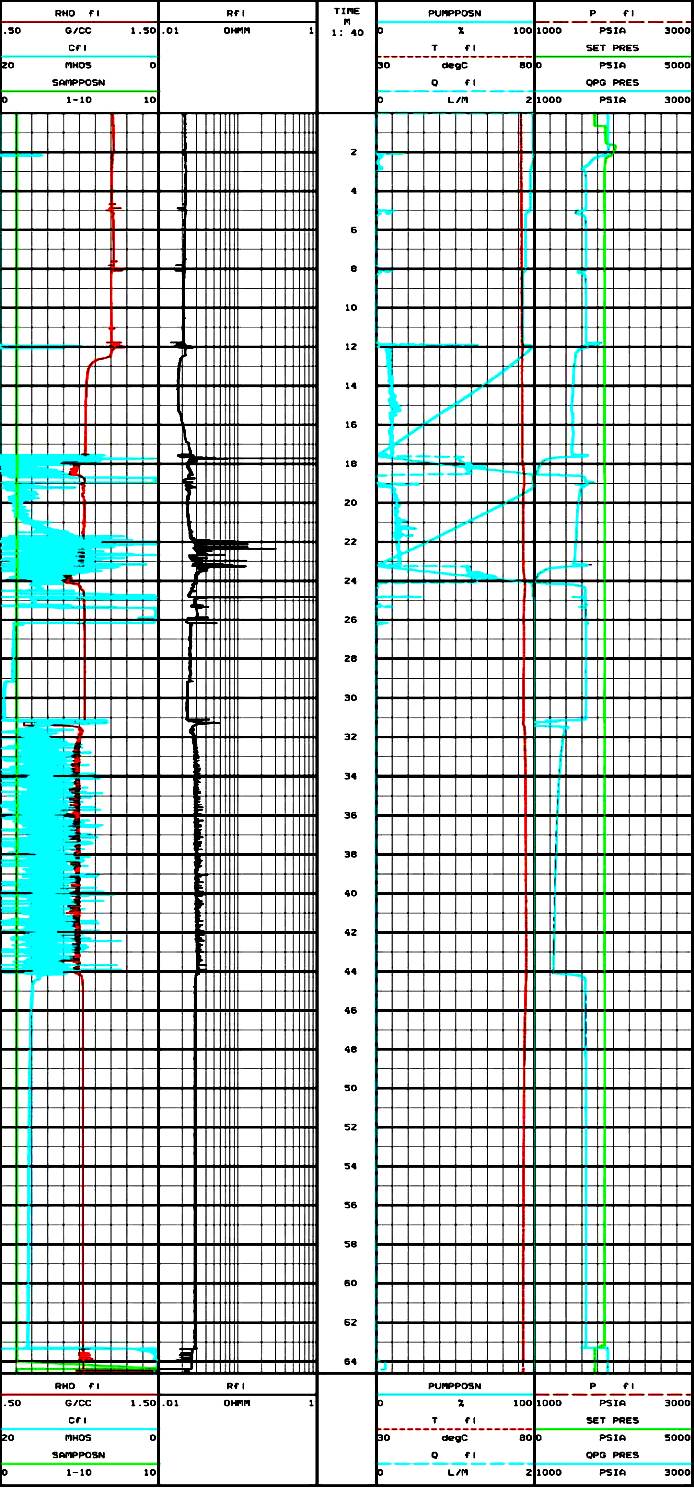
This test was the second commercial use of the SFT chambers in
conjunction with the FET. 4 litres pumped in 12 minutes before
diversion into SFT chamber. Flowing pressure is ~400 psi below shut
in pressure. Chamber filled in ~12 minutes. Note the rapid pressure
build-up when chamber fills. This is consistent with a
noncompressible fluid, water, in the tool.
|